Tre realtà differenti ma complementari tra loro, accomunate da un unico obiettivo: ideare e realizzare prodotti che possano contribuire a migliorare la qualità, la durabilità e la sicurezza delle opere in calcestruzzo: Tekna Chem, Tenso Floor e Istituto Italiano per il Calcestruzzo, ciascuno con le proprie specifiche competenze, sviluppano infatti prodotti mirati a incrementare queste tre caratteristiche. In particolare, le attività di ricerca dell’Istituto sono orientate a creare additivi che incrementino la durabilità. “In Italia i costi per la manutenzione delle opere pubbliche in calcestruzzo sono elevatissimi e incidono sempre di più sul totale delle spese da affrontare da parte dello Stato”, spiega Silvio Cocco, presidente I.I.C. “I prodotti e le nuove tecnologie da noi sviluppati consentono di incrementare la durabilità delle opere in calcestruzzo e pertanto di ridurre la manutenzione delle stesse, con il beneficio di un notevole risparmio della spesa pubblica. Nello sviluppo di nuove tecnologie non ci rivolgiamo solo al mercato italiano, siamo fortemente orientati all’estero: il nostro Gruppo è riuscito ad affrontare la difficile congiuntura economica proprio grazie alle attività commerciali in alcuni Paesi dell’Africa del Nord, in primis Algeria e Tunisia”.
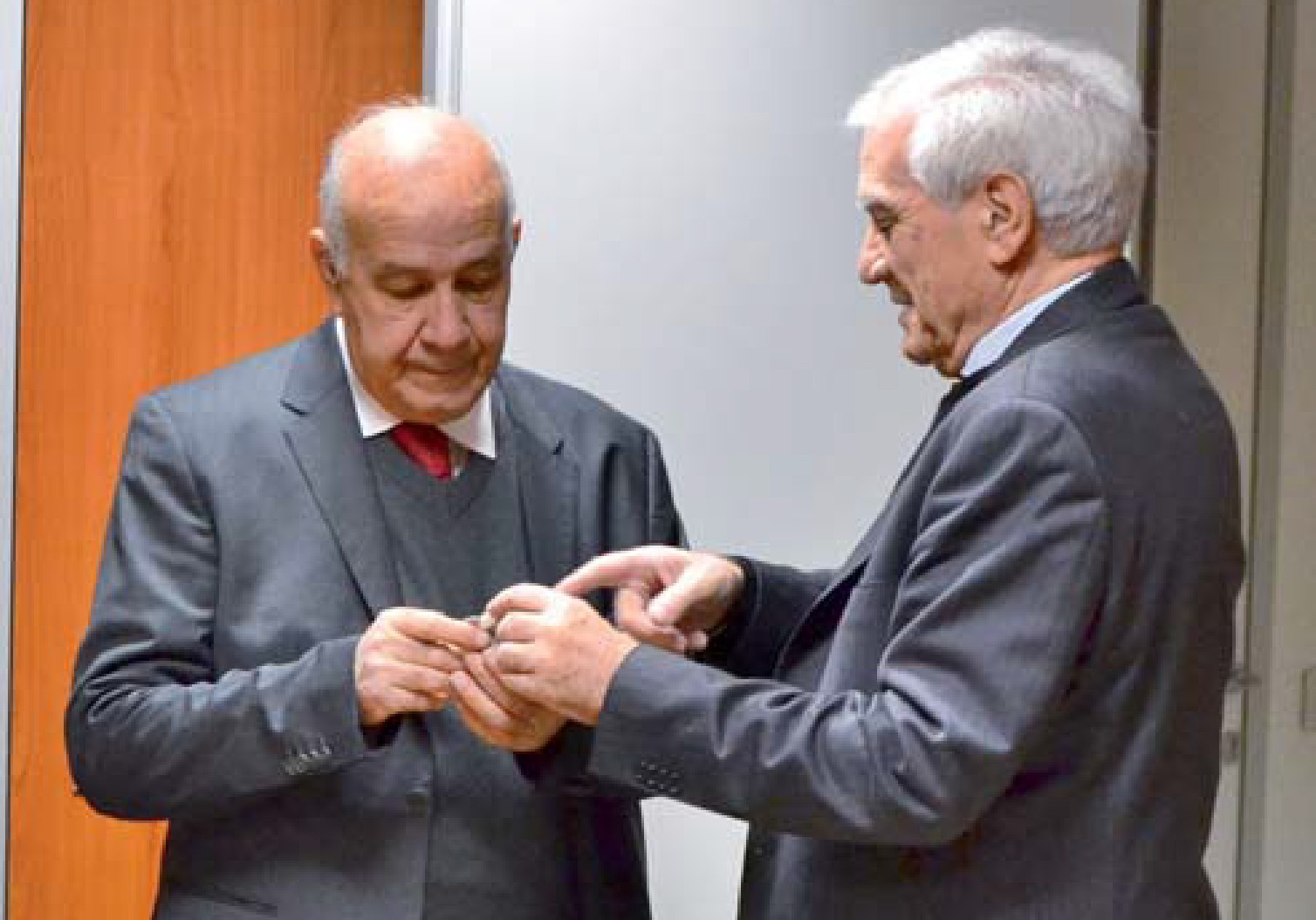
Durabilità e qualità, missioni possibili
Parlando di durabilità non si può non citare la pavimentazione senza giunti messa a punto da Tenso Floor, che permette di azzerare la manutenzione e di allungare la vita dei pavimenti industriali, e la Linea Aeternum, core business di Tekna Chem, che consente di ottenere un calcestruzzo resistente alla più alta classe di esposizione, assoluta impermeabilità, ritiri totalmente compensati, resistenze meccaniche raddoppiate, resistenza all’aggressione chimica superiore a un calcestruzzo con cementi CRS.
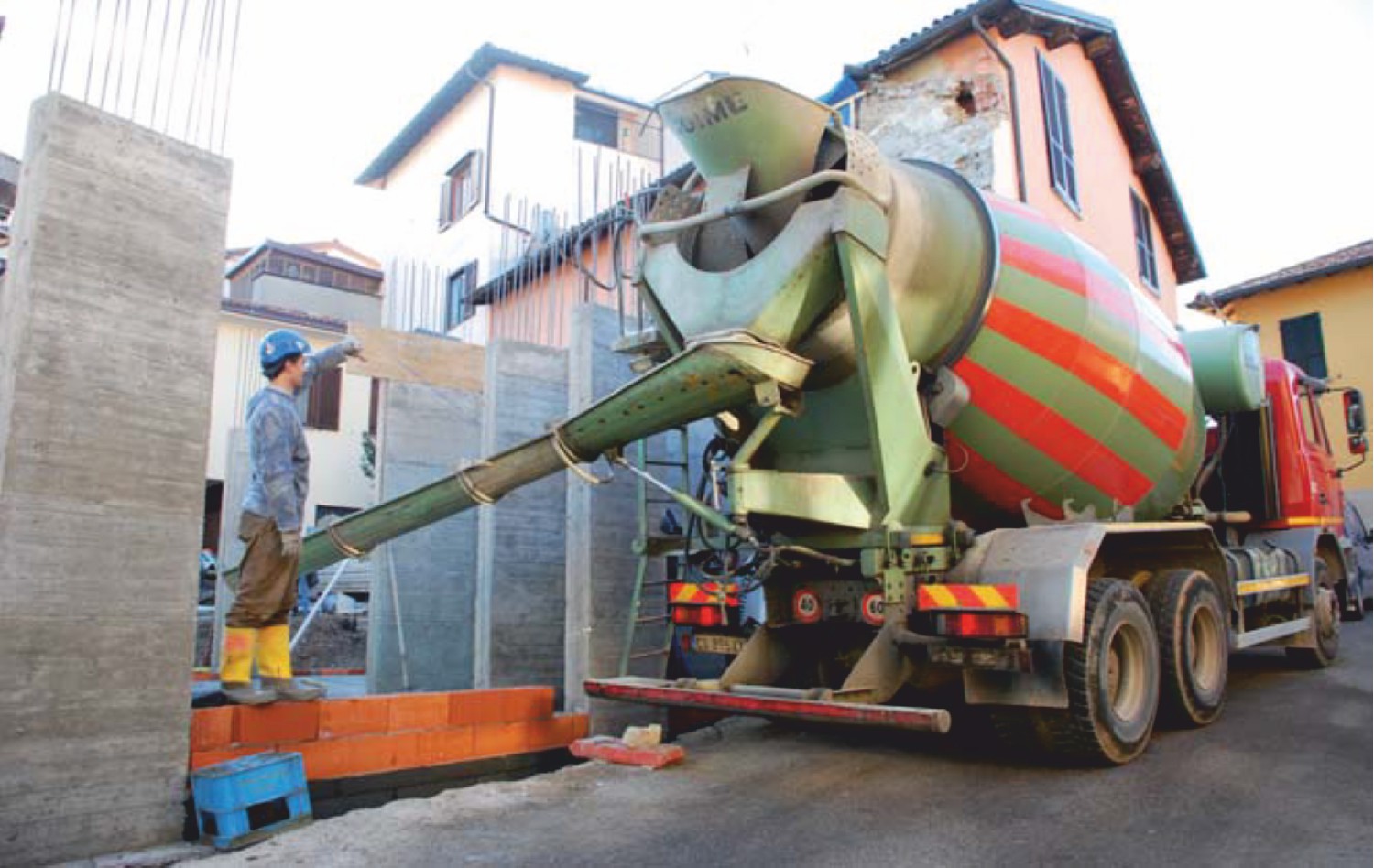
Stop alle aggiunte di acqua in cantiere
Oltre all’Aeternum, di recente Tekna Chem, tramite la ricerca effettuata dall’I.I.C., ha sviluppato un altro prodotto destinato a innovare il mercato, il riattivante di fluidità AcquaNo!. Si tratta di un compound a base di polimeri di nuova generazione specifico per aiutare calcestruzzi “bisognosi di acqua” in cantiere. In sostanza, quando ci si accorge che il calcestruzzo è in fase di inizio di gelificazione con la conseguente perdita di lavorabilità, anziché aggiungere acqua, penalizzandone notevolmente la qualità, si può ricorrere all’AcquaNo! che permette di ripristinarne la lavorabilità. “Quando viene richiesto del calcestruzzo, le centrali di betonaggio eseguono la formulazione secondo le specifiche richieste, lo preparano e lo forniscono in cantiere; spesso, ancora prima che l’autobetoniera entri in cantiere, il capocantiere indica all’autista con un gesto ormai diventato consuetudine, di aggiungere acqua, ancora prima di vedere come è il calcestruzzo stesso”, continua Cocco. “Tale acqua poi evapora e lascia dei vuoti nel calcestruzzo, creando danni all’opera (le resistenze calano in modo elevato) e modificando la formulazione stessa con cui il calcestruzzo è stato venduto.
Secondo la norma, la centrale di betonaggio risponde del calcestruzzo alla bocca di scarico, ma nel momento in cui si va ad aggiungere acqua, si va a modificare ciò che è riportato sulla fattura di acquisto: sebbene questa prassi sia considerata un reato, è davvero molto diffusa. Per ovviare a questo problema, abbiamo appunto ideato AcquaNo!, un prodotto in polvere ad alta concentrazione da aggiungere direttamente nell’autobetoniera”. Commercializzato a partire dal 2014 e contenuto in sacchetti idrosolubili, il prodotto rappresenta una sorta di cassetta di pronto soccorso in cantiere: oltre a ridare al calcestruzzo tutte le sue caratteristiche iniziali esso consente di ottenere un’elevatissima fluidificazione (senza alcuna aggiunta di acqua), un incremento del mantenimento della lavorabilità, uno sviluppo delle resistenze alle brevi e alle lunghe stagionature.
L’impiego di AcquaNo! rispetto a un calcestruzzo non additivato con esso permette di ottenere: calcestruzzi molto più lavorabili a parità di rapporto a/c; posa in opera facilitata e risposta immediata delle operazioni di vibratura; riduzione del bleeding e finiture superficiali migliori; incremento nelle resistenze iniziali e finali; riduzione dei tempi di presa in funzione delle temperature esterne e del calcestruzzo; la coazione della capacità fluidificante dell’additivo e la maggiore velocità di idratazione del cemento. Infine il rapido indurimento consente la riduzione dei tempi di scasseratura.
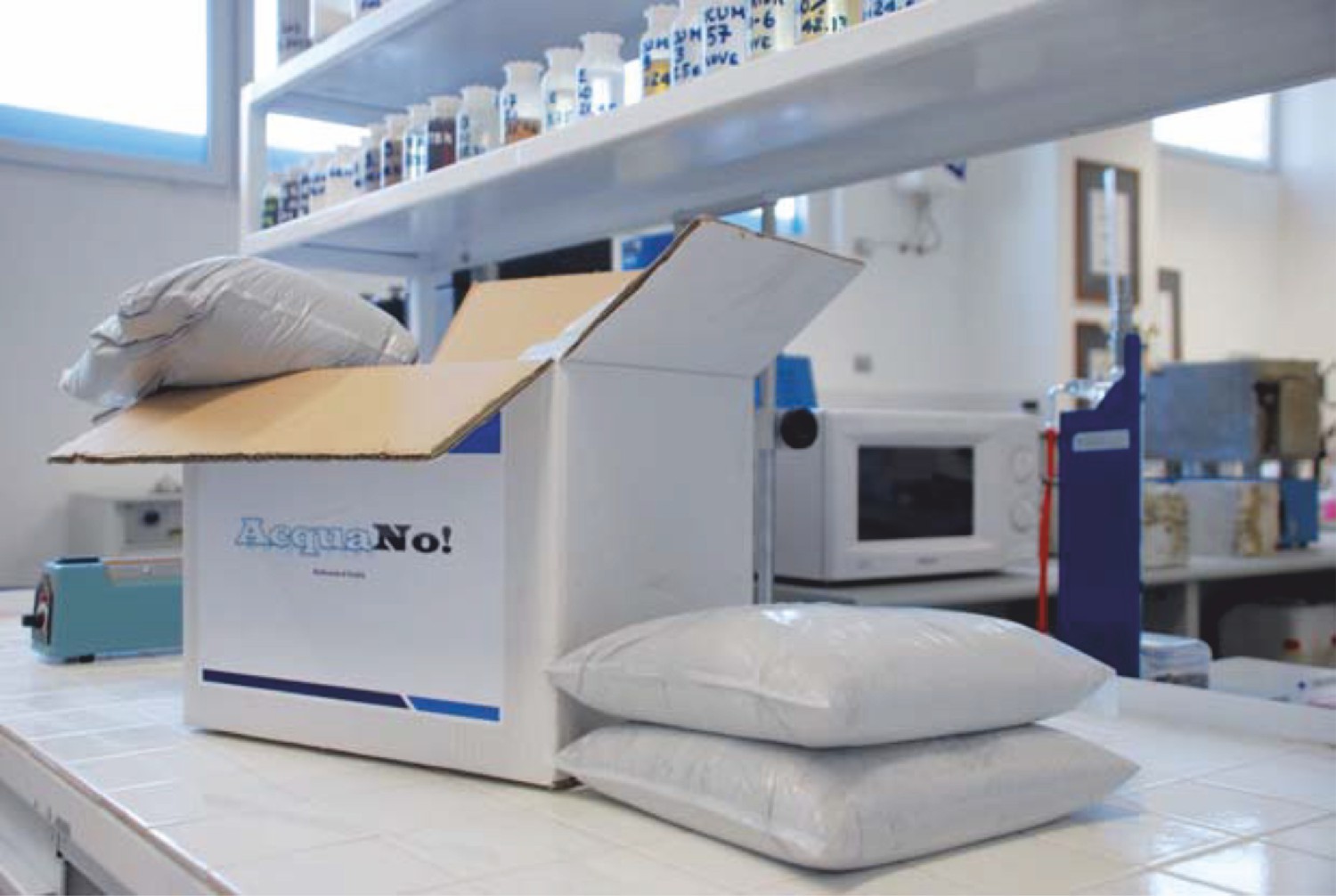
Costruzioni | Dicembre 2013