Una rete, operativa su scala nazionale, nata per sviluppare una tecnica, quella della post-tensione applicata ai pavimenti industriali, che ha già dato molti buoni frutti. Non un’associazione nel senso classico, ma un network modernamente coeso e con compiti divisi sulla base delle competenze e della specializzazione. Il 2015 si chiude con un “battesimo” che farà parlare molto di sé anche in futuro: quello di Floortek Postension Team, una squadra composta da alcune aziende specializzate in pavimenti industriali della Penisola e dal polo di Renate (Monza Brianza) di ricerca, produzione, esecuzione e controllo che gravita intorno all’Istituto Italiano per il Calce – struzzo e alle sue associate Tekna Chem e soprattutto Tensofloor, realtà nata proprio per realizzare questa innovativa tipologia di pavimentazione. L’idea nasce dal dialogo dei vertici IIC, Silvio Cocco e Valeria Campioni, con alcuni pavimentisti, strutturati anche sotto il profilo ingegneristico, che hanno puntato e puntano sull’alta specializzazione e che con questo sodalizio potranno arricchire la propria offerta anche con i pavimenti postesi.
Saranno loro a occuparsi degli aspetti esecutivi legati a getti e pose del calcestruzzo, per esempio. Tekna Chem, da parte sua, fornirà gli additivi, alla base di quell’Aeternum CAL (il calcestruzzo ideale per questa soluzione) già impiegato da Tenso floor per l’esecuzione di circa 600mila m2 di “postesi” lungo tutto lo Stivale. La stessa Tensofloor, invece, si occuperà delle lavorazioni specialistiche legate alla post-tensione: posa dei trefoli e delle testate, accurate operazioni di tesatura e via dicendo. L’Istituto, infine, avrà il compito cruciale di progettare i pavimenti (postesi, ma anche tradizionali), nonché di qualificare e controllare i materiali, dalla produzione alla betoniera, dal getto alla maturazione.
Le imprese di pavimentisti che fanno parte del Floortek Postension Team, come detto, copriranno l’intero territorio nazionale e saranno suddivise per aree: ST PAV di Treviso per il Nord, Paimo di Prato per il Centro Lazio compreso, Techno-Pavim (Napoli) per buona parte del Sud Italia e, infine, Spice di Sciacca (Agrigento) che si occuperà di Sicilia, Calabria e Basilicata.
Per la prima volta, vale la pena di sottolinearlo, il pavimento industriale posteso trova un consorzio organizzato e dedicato, in grado di sostenerne, nel modo più adeguato, la diffusione. Per il mercato è senza dubbio un’importante novità. “Per la prima volta grazie a questo network – spiega Silvio Cocco – il mercato può contare, a livello nazionale, su una soluzione altamente tecnica dove tutti i lavori (non solo quelli di post-tensione) vengono progettati. Tutto il calcestruzzo impiegato, inoltre, verrà controllato, nonché coperto da una polizza assicurativa decennale”.
Per la prima volta, in pratica, un gruppo di pavimentisti avrà dietro le spalle un vero e proprio ufficio tecnico, che si occuperà di progetto e assistenza specialistica. “Con questa iniziativa – aggiunge Cocco – rilanciamo una pratica costruttiva che ha conosciuto la prima pavimentazione progettata del genere ‘soltanto’ dieci anni fa e che troppo spesso, in passato, ha pagato dazio per la mancanza di quell’‘ingegno dell’ingegnere’ che deve accompagnare ogni intervento di qualità”.
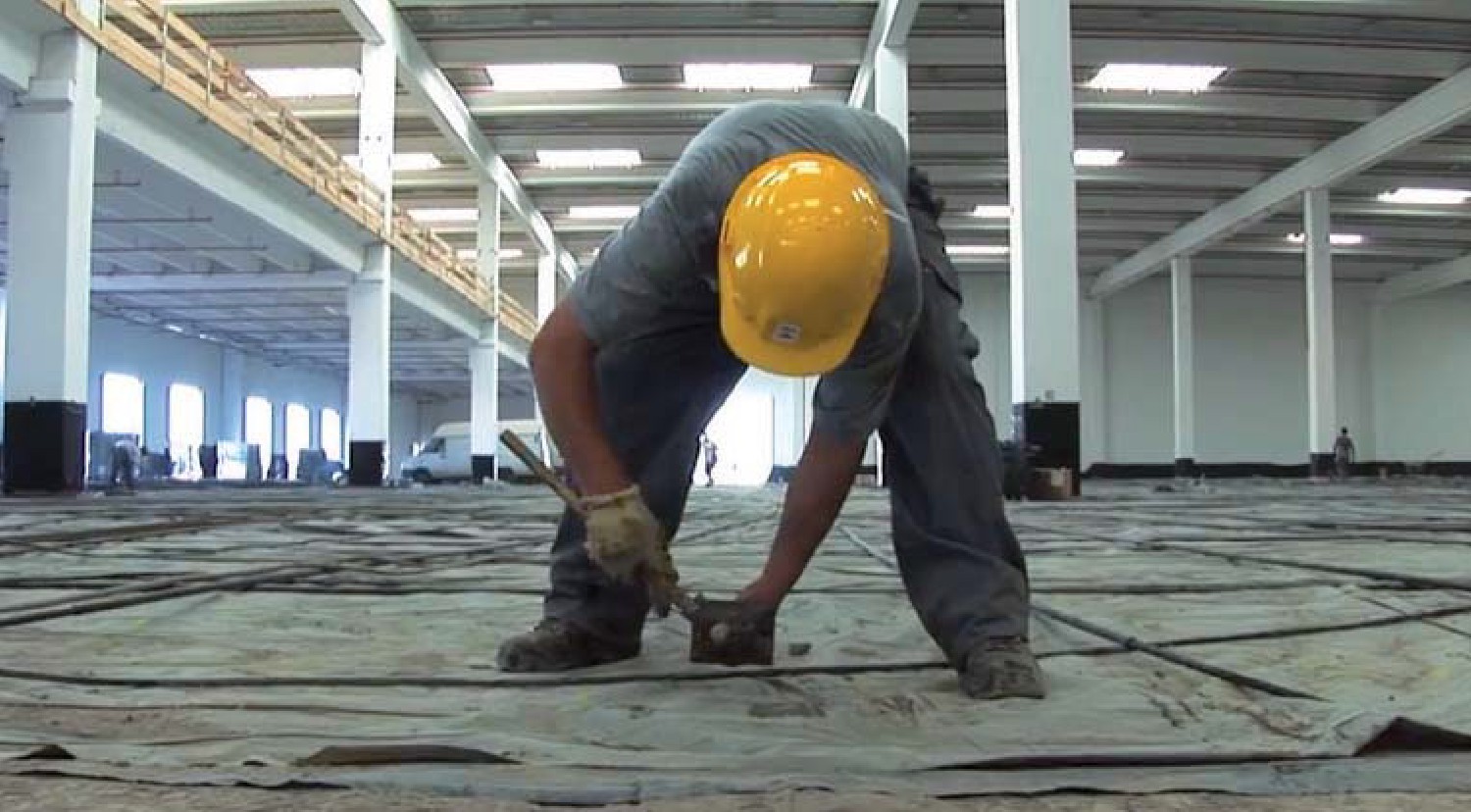
LA LEZIONE AMERICANA. E I PIONIERI DI RITORNO
Se questa è la notizia del presente, punto di partenza per una crescita della qualità del costruire nel prossimo futuro, va ricordato che il pavimento posteso non solo ha già in bacheca, nel nostro Paese, numerose applicazioni di successo, ma vanta anche una storia tecnica passata significativa, che vale la pena portare alla memoria. Tutto inizia negli anni Sessanta quando il geometra Cocco si occupa di produzione e controllo del calcestruzzo per alcuni importanti ampliamenti di piste aeroportuali (Rimini, Cameri, Cervia, Linate, Treviso e altri scali). Ci troviamo in un contesto costruttivo che, come è noto, è sempre stato “governato” da indicazioni estremamente vincolanti (in molti casi stiamo parlando di aeroporti militari, in cui l’approccio adottato era spesso e volentieri ispirato dalle norme tecniche americane) e dove i lavori diventano autentici laboratori di precisione, rigore, verifica puntuale. Ma negli stessi anni al calcestruzzo capitava di transitare dalla “nobiltà” degli aeroporti alla “miseria” dei nascenti pavimenti degli insediamenti industriali, non ancora livellati con i cosiddetti elicotteri, ma rifiniti a mano con la cazzuola americana. “Con squadre di quattro persone – racconta il geometra Cocco a COSTRUZIONI – si facevano circa 240 m2 al giorno, realizzando lunghe strisce in alternanza. A causa dei ritiri differenziati erano piuttosto diffusi, naturalmente, gli imbarcamenti”.
Negli Usa, viceversa, dove aveva sede la multinazionale del settore per cui lavorava Cocco, le medie erano di circa 900 m2 giornalieri con lavori effettuati a regola d’arte. “Durante un viaggio di studio in Canada – racconta – ho conosciuto una squadra di pavimentisti italiani che lavorava a -20°C eseguendo opere impeccabili. Li ho portati con me in Italia e insieme abbiamo realizzato un primo importante lavoro di 5.000 m2 lungo la via Emilia”. Quella squadra di emigranti di ritorno portava con sé dall’America un bagaglio di norme rigorose dettate dalle buone pratiche e insieme innovazione tecnica, il mix, insomma, alla base della qualità. Uno di loro, Luigi Barichello, aveva messo in valigia, smontata, una livellatrice a elicottero di ultima generazione, in acciaio speciale (anni dopo avrebbe fondato la Barikell, ramo elicotteri per il calcestruzzo).
In più, in un sistema sregolato conosce vano le regole del buon lavoro, che adottarono per realizzare pavimenti senza più imbarcamenti, con planarità inarrivabili e finiti a tempo di record. E fecero scuola. “Erano i tempi – continua Cocco – dei campi di getto cosiddetti ‘quadratici’: realizzavamo cioè porzioni quadrate di pavimento per bilanciare le tensioni superficiali e ridurre gli imbarcamenti. Barichello e i suoi compagni, inoltre, gettavano con un rapporto acqua-cemento molto basso, essendo abituati a lavorare nelle condizioni più gravose: allora non vi erano i calcestruzzi autocompattanti o i fluidificanti di oggi”. Quegli uomini, insomma, pionieri al contrario, scoprirono l’America a casa nostra, e cavalcarono il Boom. Il mercato, in seguito, generò costellazioni di artigiani che, con furgoncino ed elicottero, pavimentarono (più o meno bene) l’industria italiana. Prese avvio anche la stagione dell’associazionismo. Ma nonostante questo, il pavimento industriale non riuscì mai ad assurgere alla “dignità” delle strutture verticali o di altri generi costruttivi rigorosamente progettati.
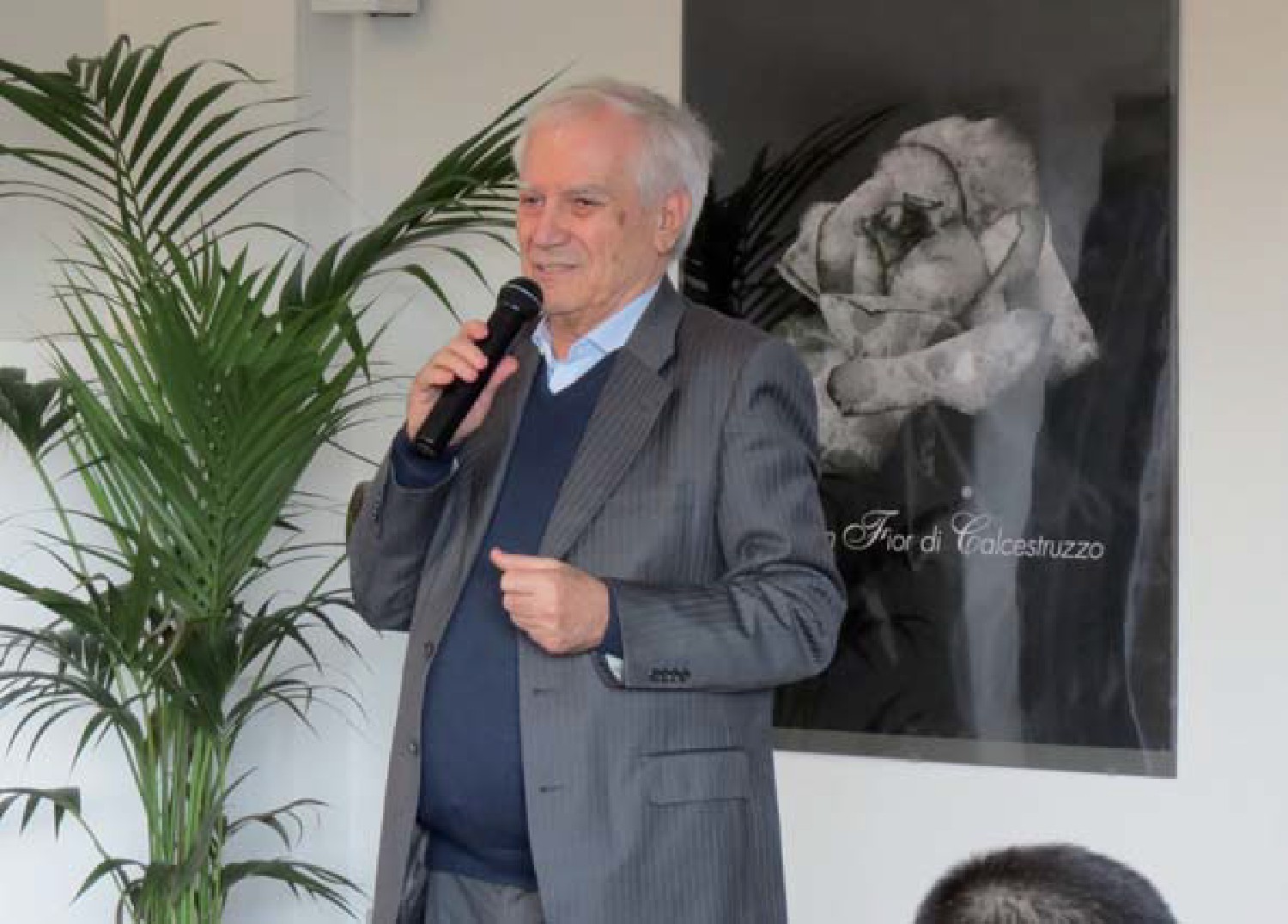
IL SALTO DI QUALITÀ DELLA POST-TENSIONE
Finché arrivò l’era della post-tensione, tecnica di cui ci siamo più volte occupati in queste stesse pagine, per esempio nei numeri di Gennaio-Febbraio e Marzo di COSTRUZIONI, raccontando la storia del decennale dalla prima importante applicazione. La sua genesi, però, deve ancora una volta partire da quell’approccio “ingegneristico” alla lavorazione e, insieme ad essa, ai materiali impiegati, che contraddistingue lo stile IIC. Un primo input arriva negli anni in cui il geometra Cocco, specialista del calcestruzzo, collabora con un produttore spagnolo di trefoli d’acciaio, la “maglia” delle strutture postese. Da qui ad approfondire la tecnica della post-tensione, molto diffusa all’estero, per esempio nella realizzazione di travi di ponti o edifici particolari, il passo è breve. Quindi, l’idea, del tutto originale: impiegare i trefoli anche nella costruzione di pavimenti industriali, trattandoli alla pari delle altre strutture postese.
Cocco entra in contatto con il colosso Bouygues Construction, che aveva acquisito VSL, azienda specializzata in “posttensioning”. Ai loro vertici presenta un “concept” di pavimento posteso, che intriga tecnicamente ma non entusiasma per prospettive commerciali. Dopo qualche tempo, però, alcuni ingegneri argentini di VSL tirano fuori dal cassetto il progetto di Cocco, lo aggiornano con un opportuno software di calcolo e realizzano uno dei capisaldi internazionali del genere, un pavimento costellato da pilastri di 400.000 m2 per uno stabilimento Nestlè in Cile. La VSL mette quindi a disposizione di Cocco il software di calcolo. Parte la stagione delle prove (per esempio un pavimento di 800 m2 per la Pama Prefabbricati a Maclodio, Brescia), quindi il primo grande lavoro: 12.000 m2 per il magazzino merci della Tenax, a Viganò, in Brianza, nel 2005. “Dopo dieci anni – fanno sapere proprio da Tenax – quel pavimento è come nuovo, perfettamente planare e in grado di evitare ai nostri carrelli robotizzati il minimo sobbalzo. E questo ci ha sempre consentito di aumentare velocità e produzione, senza mai far cadere le merci”. Le ruote dei carrelli, aggiungono da Tenax, “non sono mai state sostituite in quanto la planarità ha fatto sì che non si consumassero, e gli stessi robot non hanno mai avuto bisogno di manutenzione”.
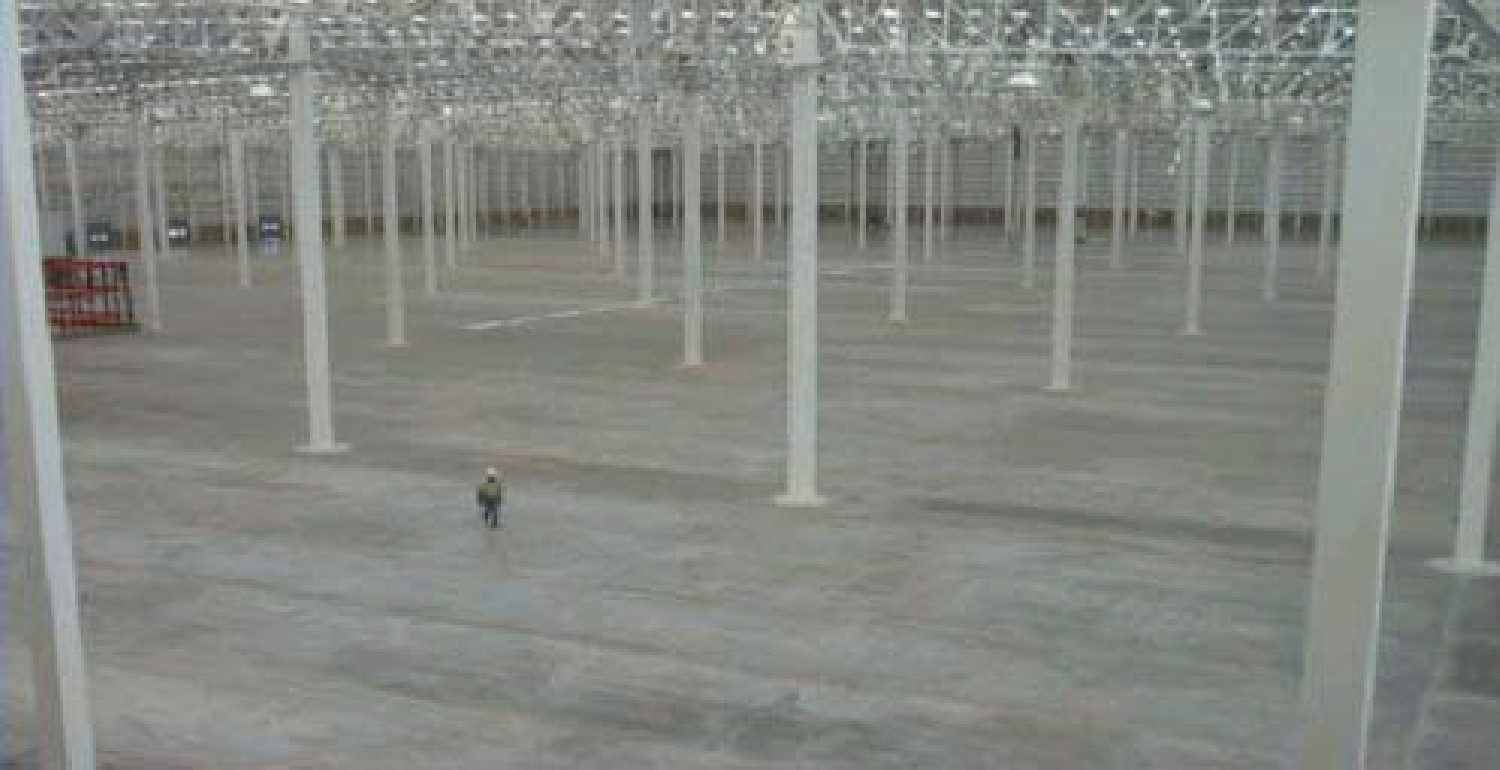
LA NASCITA DEL FLOORTEK POSTENSION TEAM
Oggi sono oltre 600.000 i metri quadrati di posteso realizzati in dieci anni da Tensofloor in tutta Italia. Con criticità e difetti pari a zero. Il merito di questo risultato va alla perizia esecutiva ma anche all’impiego di un materiale specifico, costantemente innovato, il calcestruzzo Aeternum CAL: estremamente lavorabile e molto vicino a un autocompattante, non prevede l’aggiunta di acqua in cantere ed è sottoposto a continui controlli in ogni fase del suo percorso dalla centrale di betonaggio al suolo (e, essendo il processo di tesatura articolato in più fasi, anche dopo). Il suo “cuore” tecnico sono gli additivi che formano il compound Aeternum che consentono di incrementare le resistenze o modificare la presa a seconda della stagione. Aeternum CAL si è dunque dimostrato la “sostanza” ideale per mettere in “forma” pavimenti industriali postesi di prima classe, senza giunti, imbarcamenti e fessurazioni, molto diffusi tra l’altro, proprio per la loro impermeabilità totale garantita da questo calcestruzzo, anche nei progetti di piattaforme ecologiche. Ora prodotti e tecnica diventano strumenti messi a disposizione di una nuova squadra, il Floortek Postension Team, che coprirà l’intero territorio nazionale: “Per completare il quadro, ma ci stiamo lavorando- concludere il geometra Cocco -, andrebbe costituito un network nazionale, in rete con noi, di centrali di betonaggio qualificate per produrre Aeternum CAL. Quel che già si può toccare con mano, comunque, è questo calcestruzzo stabile, impermeabile, controllato per quanto riguarda i ritiri, con rischi di fessurazioni ridotti a zero e resistenze incrementabili, nonché in grado di contrastare le aggressioni di cloruri e solfati”.
Progettato, controllato, garantito e anche assicurato, per la precisione grazie a una copertura stipulata con la Reale Mutua. La qualità sembra avere proprio trovato il suo fondamento, che fa rima con pavimento. Naturalmente posteso.
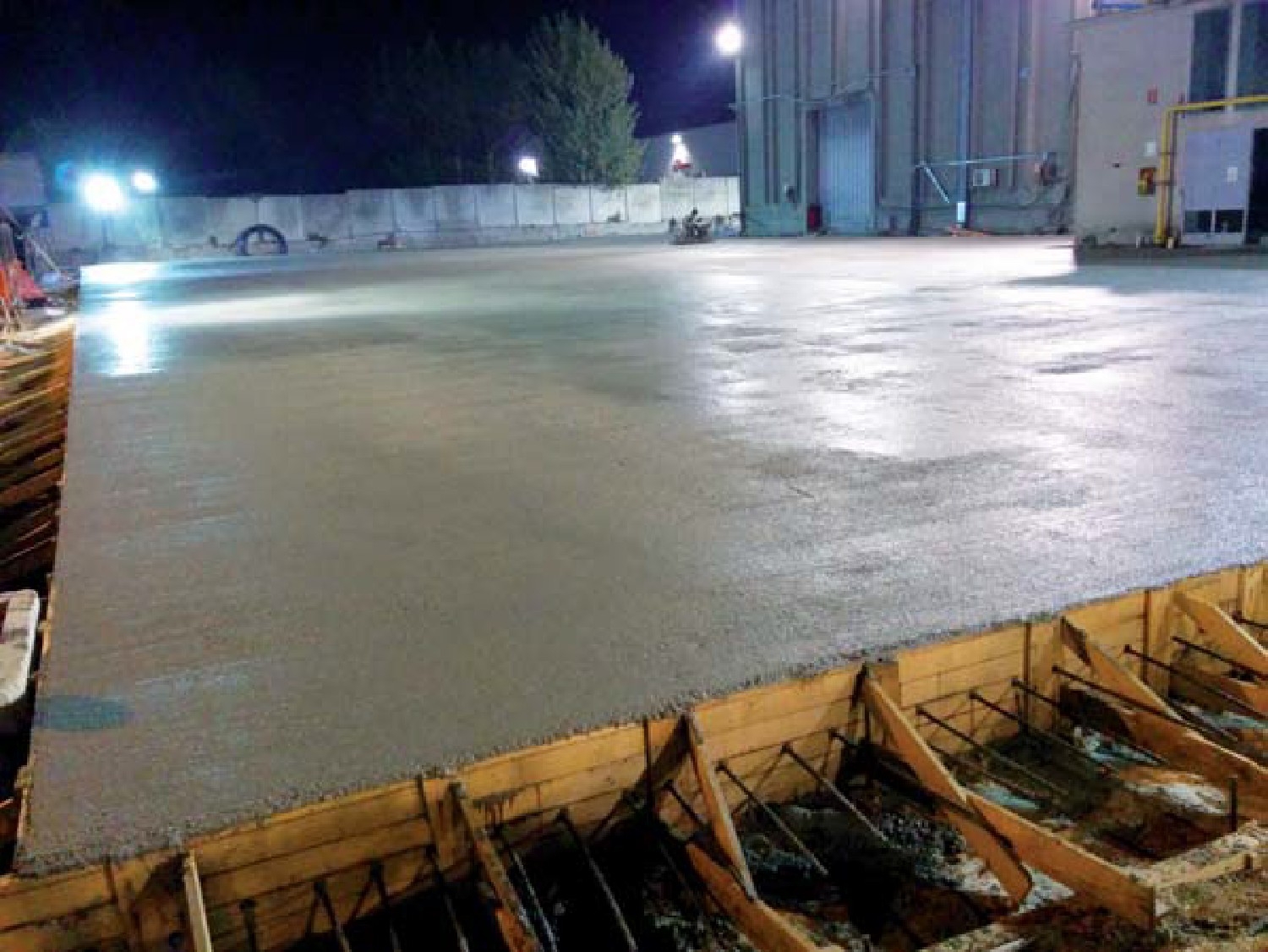
Fabrizio Apostolo
Costruzioni – dicembre 2015